New challenges for automotive wiring harness management.
The Giantlok cable & wiring automotive solution focuses on delivering the standards and objectives while optimizing your harness processes.
Case Background
Taiwan boasts the world’s highest motor scooters density rate. The demand and competition in Taiwan’s electric scooters market has been heating up in last two years as a consequence of the maturity of the power supply infrastructure and the incentive from government subsidization. The well-known electric scooter brand who had revolutionized the scooter’s landscape in Taiwan, faced challenges for shorter iterations of development cycles as well as better performance on new model introductions.
Business Challenges
Electric vehicles deployment has been growing rapidly over the past decade and urged governments around the world to increase awareness and embrace the benefits of electric vehicles to reduce oil consumption, air pollution, and toxic emissions. However, the fast-growing introduction of new technologies into the automotive market also lead to a multitude of challenges for harness management. In Taiwan, the electric scooters gained ground with every year a new record being set for the number of electric scooters on the nation’s streets. Startup electric scooter companies faced the challenges on how to reduce harness manufacturing turnaround, time and costs to couple with scalability, reliability and improvements to high efficiency, while also meeting the time-to-market new models development cycles.
Strategic Objectives
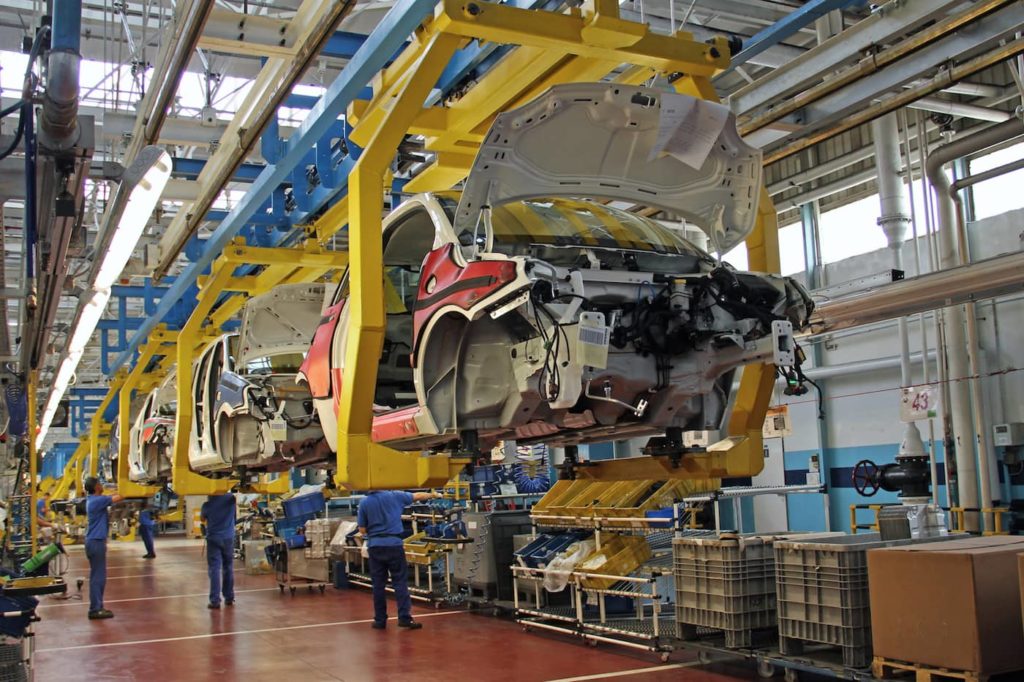
Giantlok Solution
The Giantlok cable & wiring automotive solution focuses on delivering the standards and objectives while optimizing your harness processes.
We ensure you get peace-of-mind with products manufactured in ISO-certified facilities and verified by third party labs to meet performance standards. We know just what it takes to develop and manage a successful automotive project. The Giantlok tailored solution addresses the following highlights:
– By teaming up with customers – and backed up by 40 years of experience, it enables us to configure a set of portfolios from protected routing of cables right from exterior through interior of high-performance engine compartment which have proven outcomes relating ultra-heat resistance, vibration resistance, leak prevention, abrasion protection, and slip resistance to answer the challenges in automotive industry.
– Giantlok accommodates the consulting service to examine and walk through the potential safety and approval-relevant weaknesses early in your development phase to avoid costly rework and delays.
– The safety of passengers is in our good hand with all the components been tested extensively and demonstrating high quality which are recognized under globally certification mark to make you competitive in your global business environment.
– With Giantlok, you can increase efficiency by working with an expert partner start from development phase and ensure the development time is well controlled, installation is optimized and further the harness processes can be easily standardized.
Business Benefits
The reliable, engineered and affordable portfolios addressed the automotive manufacturer’s needs for a standardized harness process that improves efficiency and facilitates turnaround time and costs. With our well-established product offerings, you can optimize maintenance and operations planning, reduce lifecycle costs through longer service and maintenance intervals. Our industrial insight and proven track record has ensures that we play a central role in shaping the automotive harness landscape of the future and lead the way to your sustainable mobility.